1, అలసటతో కూడిన దుస్తులు
దీర్ఘకాలిక లోడ్ ఆల్టర్నేటింగ్ ప్రభావం కారణంగా, భాగం యొక్క పదార్థం విరిగిపోతుంది, దీనిని ఫెటీగ్ వేర్ అంటారు. పగుళ్లు సాధారణంగా మెటల్ లాటిస్ నిర్మాణంలో చాలా చిన్న పగుళ్లతో ప్రారంభమవుతాయి మరియు తరువాత క్రమంగా పెరుగుతాయి.
పరిష్కారం: భాగాల ఒత్తిడి సాంద్రతను వీలైనంత వరకు నిరోధించాలని గమనించాలి, తద్వారా సరిపోలే భాగాల గ్యాప్ లేదా బిగుతును అవసరాలకు అనుగుణంగా పరిమితం చేయవచ్చు మరియు అదనపు ప్రభావ శక్తి తొలగించబడుతుంది.
2, ప్లాస్టిక్ దుస్తులు
ఆపరేషన్లో, జోక్యం ఫిట్ భాగం ఒత్తిడి మరియు టార్క్ రెండింటికీ లోనవుతుంది. రెండు శక్తుల చర్యలో, భాగం యొక్క ఉపరితలం ప్లాస్టిక్ వైకల్యానికి గురయ్యే అవకాశం ఉంది, తద్వారా ఫిట్ బిగుతు తగ్గుతుంది. జోక్యం ఫిట్ను గ్యాప్ ఫిట్గా మార్చడం కూడా సాధ్యమే, ఇది ప్లాస్టిక్ దుస్తులు. బేరింగ్ మరియు జర్నల్లోని స్లీవ్ హోల్ జోక్యం ఫిట్ లేదా ట్రాన్సిషన్ ఫిట్ అయితే, ప్లాస్టిక్ వైకల్యం తర్వాత, అది బేరింగ్ లోపలి స్లీవ్ మరియు జర్నల్ మధ్య సాపేక్ష భ్రమణ మరియు అక్షసంబంధ కదలికకు దారి తీస్తుంది, ఇది షాఫ్ట్ మరియు షాఫ్ట్లోని అనేక భాగాలను ఒకదానికొకటి మార్చుకోవడానికి దారితీస్తుంది మరియు సాంకేతిక స్థితిని క్షీణిస్తుంది.
పరిష్కారం: యంత్రాన్ని రిపేర్ చేసేటప్పుడు, జోక్యం ఫిట్టింగ్ భాగాల కాంటాక్ట్ ఉపరితలాన్ని జాగ్రత్తగా తనిఖీ చేయడం అవసరం, అది ఏకరీతిగా ఉందో లేదో మరియు నిబంధనలకు అనుగుణంగా ఉందో లేదో నిర్ధారించుకోవాలి. ప్రత్యేక పరిస్థితులు లేకుండా, జోక్యం ఫిట్ భాగాలను ఇష్టానుసారంగా విడదీయలేరు.
3、గ్రౌండింగ్ రాపిడి
భాగాలకు తరచుగా ఉపరితలంపై చిన్న గట్టి అబ్రాసివ్లు జతచేయబడి ఉంటాయి, దీని ఫలితంగా భాగం యొక్క ఉపరితలంపై గీతలు లేదా గీతలు ఏర్పడతాయి, దీనిని మనం సాధారణంగా రాపిడి దుస్తులుగా పరిగణిస్తాము. వ్యవసాయ యంత్ర భాగాల యొక్క ప్రధాన దుస్తులు అబ్రాసివ్ దుస్తులు, ఉదాహరణకు ఫీల్డ్ ఆపరేషన్ ప్రక్రియలో, వ్యవసాయ యంత్రాల ఇంజిన్ తరచుగా గాలిలో చాలా ధూళిని ఇన్టేక్ ఎయిర్ ఫ్లోలో కలుపుతుంది మరియు పిస్టన్, పిస్టన్ రింగ్ మరియు సిలిండర్ వాల్ అబ్రాసివ్తో పొందుపరచబడతాయి, పిస్టన్ కదలిక ప్రక్రియలో, తరచుగా పిస్టన్ మరియు సిలిండర్ గోడను గీతలు పడతాయి. పరిష్కారం: గాలి, ఇంధనం మరియు చమురు ఫిల్టర్లను సకాలంలో శుభ్రం చేయడానికి మీరు డస్ట్ ఫిల్టర్ పరికరాన్ని ఉపయోగించవచ్చు మరియు ఉపయోగించాల్సిన ఇంధనం మరియు నూనె అవక్షేపించబడతాయి, ఫిల్టర్ చేయబడతాయి మరియు శుభ్రం చేయబడతాయి. రన్-ఇన్ పరీక్ష తర్వాత, ఆయిల్ పాసేజ్ను శుభ్రం చేయడం మరియు ఆయిల్ను భర్తీ చేయడం అవసరం. యంత్రాల నిర్వహణ మరియు మరమ్మత్తులో, కార్బన్ తొలగించబడుతుంది, తయారీలో, పదార్థాల ఎంపిక అధిక దుస్తులు నిరోధకతను కలిగి ఉండాలి, తద్వారా భాగాల ఉపరితలం వారి స్వంత దుస్తులు నిరోధకతను మెరుగుపరచడానికి ప్రోత్సహించబడుతుంది.
4, యాంత్రిక దుస్తులు
యాంత్రిక భాగం యొక్క మ్యాచింగ్ ఖచ్చితత్వం ఎంత ఎక్కువగా ఉన్నా, లేదా ఉపరితల కరుకుదనం ఎంత ఎక్కువగా ఉన్నా. మీరు తనిఖీ చేయడానికి భూతద్దాన్ని ఉపయోగిస్తే, ఉపరితలంపై చాలా అసమాన ప్రదేశాలు ఉన్నాయని మీరు కనుగొంటారు, భాగాల సాపేక్ష కదలిక ఈ అసమాన ప్రదేశాల పరస్పర చర్యకు దారితీసినప్పుడు, ఘర్షణ చర్య కారణంగా, భాగాల ఉపరితలంపై లోహాన్ని తొక్కడం కొనసాగిస్తుంది, ఫలితంగా భాగాల ఆకారం, వాల్యూమ్ మొదలైనవి మారుతూనే ఉంటాయి, ఇది యాంత్రిక దుస్తులు. యాంత్రిక దుస్తులు మొత్తం లోడ్ మొత్తం, భాగాల ఘర్షణ సాపేక్ష వేగం వంటి అనేక అంశాలకు సంబంధించినది. ఒకదానికొకటి వ్యతిరేకంగా రుద్దుకునే రెండు రకాల భాగాలు వేర్వేరు పదార్థాలతో తయారు చేయబడితే, అవి చివరికి వేర్వేరు మొత్తంలో దుస్తులు ధరిస్తాయి. యాంత్రిక దుస్తులు రేటు నిరంతరం మారుతూ ఉంటుంది.
యంత్రాల వాడకం ప్రారంభంలో, తక్కువ రన్-ఇన్ వ్యవధి ఉంటుంది మరియు ఈ సమయంలో భాగాలు చాలా వేగంగా ధరిస్తాయి; ఈ కాలం తర్వాత, భాగాల సమన్వయం ఒక నిర్దిష్ట సాంకేతిక ప్రమాణాన్ని కలిగి ఉంటుంది మరియు యంత్రం యొక్క శక్తికి పూర్తి ఆటను ఇవ్వగలదు. ఎక్కువ కాలం పనిచేసే కాలంలో, యాంత్రిక దుస్తులు సాపేక్షంగా నెమ్మదిగా మరియు సాపేక్షంగా ఏకరీతిగా ఉంటాయి; ఎక్కువ కాలం యాంత్రిక ఆపరేషన్ తర్వాత, భాగాల దుస్తులు మొత్తం ప్రమాణాన్ని మించిపోతుంది. దుస్తులు పరిస్థితి క్షీణించడం మరింత దిగజారుతుంది మరియు భాగాలు తక్కువ సమయంలో దెబ్బతింటాయి, ఇది తప్పు దుస్తులు కాలం. పరిష్కారం: ప్రాసెస్ చేస్తున్నప్పుడు, భాగాల యొక్క ఖచ్చితత్వం, కరుకుదనం మరియు కాఠిన్యాన్ని మరింత మెరుగుపరచడం అవసరం మరియు వినియోగ పరిస్థితులను మెరుగుపరచడానికి మరియు ఆపరేటింగ్ విధానాలను ఖచ్చితంగా అమలు చేయడానికి సంస్థాపన ఖచ్చితత్వాన్ని కూడా మెరుగుపరచాలి. భాగాలు ఎల్లప్పుడూ సాపేక్షంగా మంచి లూబ్రికేషన్ స్థితిలో ఉండేలా చూసుకోవాలి, కాబట్టి యంత్రాలను ప్రారంభించేటప్పుడు, మొదట తక్కువ వేగంతో మరియు తక్కువ లోడ్తో కొంత సమయం పాటు నడపండి, పూర్తిగా ఆయిల్ ఫిల్మ్ను ఏర్పరుచుకోండి, ఆపై యంత్రాలను సాధారణంగా నడపండి, తద్వారా భాగాల దుస్తులు తగ్గించవచ్చు.
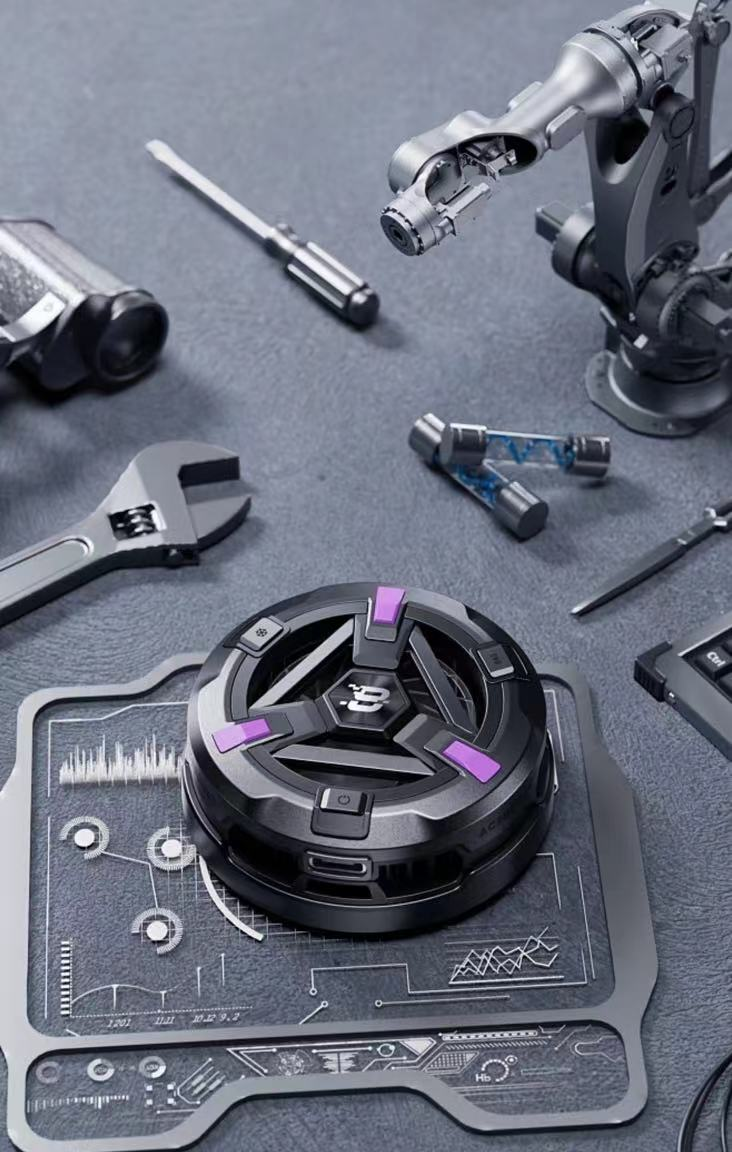
పోస్ట్ సమయం: మే-31-2024